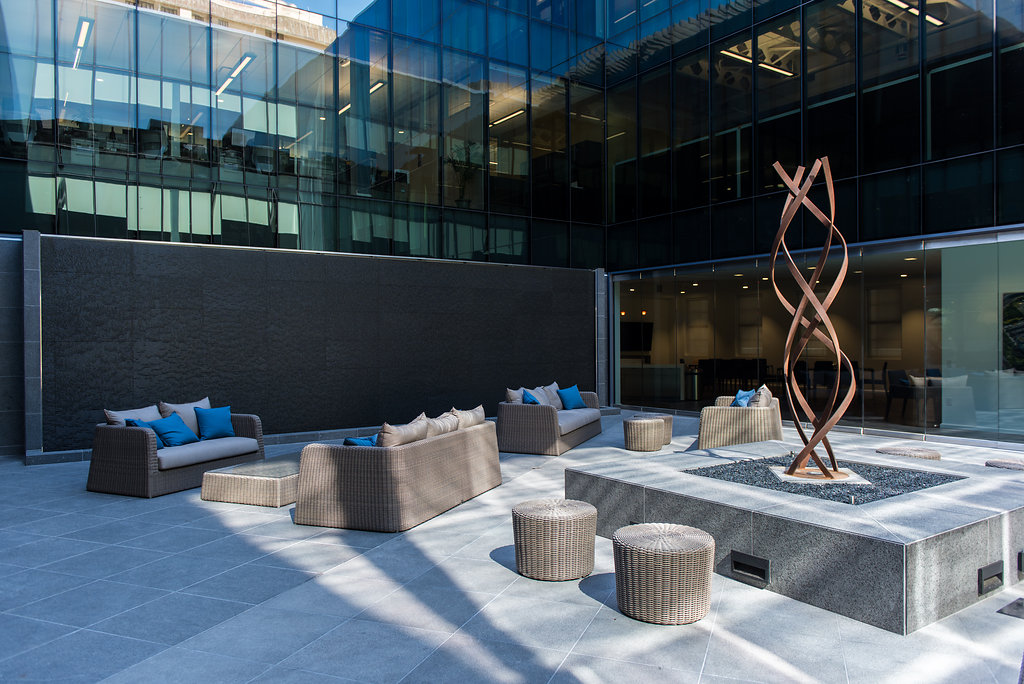
REFERENCES
American Architectural Manufacturers Association (AAMA):
- AAMA/NWWDA 101/I.S. 2-97 - Voluntary Specification, Performance Requirements and Test Procedures for Air Leakage Resistance, Water Penetration Resistance, Structural Loading, Forced Entry Resistance.
- AAMA-501.1 - Standard Test Method for Water Penetration of Windows, Curtain Walls and Doors Using Dynamic Pressure
- AAMA 501.4 - Recommended Static Test Method for Evaluating Curtain Wall and Storefront Systems Subjected to Seismic and Wind Induced Interstory Drifts.
- AAMA 2605 - Voluntary Specification, Performance Requirements and Test Procedures for Superior Performing Organic Coatings on Aluminum Extrusions and Panels.
ASTM International (ASTM):
- ASTM B 221 - Standard Specification for Aluminum and Aluminum-Alloy Extruded Bars, Rods, Wire, Profiles, and Tubes.
- ASTM E 283 - Test Method for Determining the Rate of Air Leakage Through Exterior Windows, Curtain Walls, and Doors under Specified Pressure Differences across the Specimen.
- ASTM E330 - Standard Test Method for Structural Performance of Exterior Windows, Doors, Skylights and Curtain Walls by Uniform Static Air Pressure Difference.
- ASTM E 331 - Test Method for Water Penetration of Exterior Windows, Curtain Walls, and Doors by Uniform Static Air Pressure Difference.
- ASTM E 1886 - Standard Test Method for Performance of Exterior Windows, Curtain Walls, Doors, and Impact Protective Systems Impacted by Missile(s) and Exposed to Cyclic Pressure Differentials.
- ASTM E 1996 - Standard Specification for Performance of Exterior Windows, Curtain Walls, Doors and Impact Protective Systems Impacted by Windborne Debris in Hurricanes.
National Fenestration Rating Council (NFRC):
- NFRC-100 - Procedure for Determining Fenestration Product U-factors.
- NFRC-200 - Procedure for Determining Fenestration Product Solar Heat Gain Coefficient and Visible Transmittance at Normal Incidence.
SUBMITTALS
- Submit under provisions of applicable Requirements.
- Product Data: Manufacturer's data sheets on each product to be used, including:
- Preparation instructions and recommendations.
- Storage and handling requirements and recommendations.
Installation methods.
- Shop Drawings:
- Provide drawings showing each configuration.
- Selection Samples: For each finish product specified, two complete sets of color chips representing manufacturer's full range of available colors and patterns.
- Verification Samples: For each finish product specified, two samples, minimum size 6 inches (150 mm) square representing actual product, color, and patterns.
QUALITY ASSURANCE
- Manufacturer Qualifications: Minimum 5 year experience manufacturing similar products.
- Installer Qualifications: Minimum 2 year experience installing similar products.
- Mock-Up: Provide a mock-up for evaluation of surface preparation techniques and application workmanship.
- Finish areas designated by Architect.
- Do not proceed with remaining work until workmanship is approved by Architect.
- Refinish mock-up area as required to produce acceptable work.
PRE-INSTALLATION MEETINGS
- Convene minimum two weeks prior to starting work of this section.
DELIVERY, STORAGE, AND HANDLING
- Deliver and store products in manufacturer's unopened packaging bearing the brand name and manufacturer's identification until ready for installation.
- Handling: Handle materials to avoid damage.
PROJECT CONDITIONS
- Maintain environmental conditions (temperature, humidity, and ventilation) within limits recommended by manufacturer for optimum results. Do not install products under environmental conditions outside manufacturer's recommended limits.
SEQUENCING
- Ensure that products of this section are supplied to affected trades in time to prevent interruption of construction progress.
- Acceptable Manufacturer: PRL Glass Systems, Inc., which is located at: 13644 Nelson Ave.; City of Industry, CA 91746; Toll Free Tel: 800-433-7044; Fax: 626-968-9256; Email:request info (info@prlglass.com); Web:prlglass.com
- Substitutions: Not permitted.
- Requests for substitutions will be considered in accordance with provisions of Section 01 60 00 - Product Requirements.
- CURTAIN WALLS
- Frame : 2-1/2 inches (64 mm) face width:
- Glazing: Structural glaze verticals.
- Glazing: Structural glaze horizontals.
6 Inches (152 mm) Depth:
- Acceptable Manufacturer: PRL Glass Systems, Inc., which is located at: 13644 Nelson Ave.; City of Industry, CA 91746; Toll Free Tel: 800-433-7044; Fax: 626-968-9256; Email:request info (info@prlglass.com); Web:prlglass.com
- Substitutions: Not permitted.
- Requests for substitutions will be considered in accordance with provisions of Section 01 60 00 - Product Requirements.
- CURTAIN WALLS
- Frame : 2-1/2 inches (64 mm) face width:
- Glazing: Structural glaze verticals.
- Glazing: Structural glaze horizontals.
7 Inches (178 mm) Depth:
Product: PLCW-600 as manufactured by PRL Glass Systems, Inc.
- Performance:
- Air infiltration: Limit air leakage through fixed glazing and frames to 0.026 cfm/ft2/min (0.01 L/s/m2) when tested in accordance with ASTM E-283-04 at a cross pressure of 6.24 psf (0.30 kPa).
- Water Penetration under Static Pressure: System shall not evidence uncontrolled water penetration at a cross pressure of 15 psf (103 kPa) when tested in accordance with ASTM-E331-00.
- Water Penetration under Dynamic Pressure: System shall not evidence uncontrolled water penetration at a cross pressure of 15 psf (103 kPa) when tested in accordance with AAMA-501.1-05.
- Design Wind Load: Limit mullion deflection to L/175 up to 13 feet-6 inches (4115 mm) and L/240+1/4 inch (6 mm) for spans above 13 feet-6 inches (4115 mm) when measured in accordance with ASTM E330-02 at a cross pressure of 40 psf (276 kPa).
- Seismic Racking: Compliance that system can accommodate a lateral movement of 3/4 inch (19 mm) when tested to AAMA 501.4-00.
- Thermal Conductance: Whole product rating shall be determined in accordance with NFRC-100. Show that specified product can achieve U-factor of no greater than 0.37 (Values based on structural glaze verticals, and insulated glass comprising exterior light of 1/4 inch (6 mm) bronze, 1/2 inch (13 mm) space with argon fill and an interior light of 1/4 inch (6 mm) SunGuard SNX 62/27).
- Solar Heat Gain: Whole product rating shall be determined in accordance with NFRC-200. Show that the specified product can achieve a SHGC of no greater than 0.36. (Values based on structural glaze verticals, and insulated glass comprising exterior light of 1/4 inch (6 mm) bronze, 1/2 inch (13 mm) space with argon fill and an interior light of 1/4 inch (6 mm) SunGuard SNX 62/27).
- Large Missile Impact: Design and fabrication shall meet the performance requirements in the referenced test procedures for a +1676/-2873 Pa (+35/-60 psf) design pressure with missile impacts corresponding to Missile Level D and Wind Zone 3 for a Basic Protection Rating. (Laminated I.G. 1-1/8 inches (29 mm) I.G. Marine glazed into a rubber glazing gasket.
MATERIALS
- Material: Frames, assembly clips, trims and miscellaneous extrusions shall be extruded from Aluminum 6063-T6 alloy.
- Glazing Gaskets:
- Compression type gaskets. Extruded EPDM (Ethylene Propylene Diene Monomer) push in place gasket. Dense 60 Durometer Shore "A" - ASTM C864 Option II
- Structural silicone compatible gasket: true silicone gasket -70 Durometer Shore "A", complying with ASTM C1115, Type C.
- Thermal isolators: extruded rigid Geon complying with AAMA-303 and ASTM-D-1784-9.
- End Dams: Pre-molded end dams made from closed cell EPDM (Ethylene Propylene Diene Monomer) sponge to ASTM C509.
Class II clear anodized aluminum shall conform to AA-M12-C22-A31.
Class I clear anodized aluminum shall conform to AA-M12-C22-A41.
Class II color anodized aluminum shall conform to AA-M12-C22-A34.
Class I color anodized aluminum shall conform to AA-M12-C22-A44.
Class I clear anodized aluminum shall conform to AA-M12-C22-A41.
Class II color anodized aluminum shall conform to AA-M12-C22-A34.
Class I color anodized aluminum shall conform to AA-M12-C22-A44.
- Color: Champagne.
- Color: Light Bronze.
- Color: Medium Bronze.
- Color: Dark Bronze.
- Color: Black.
Fluorocarbon finish complying with AAMA 2605.
- Resin: 70% PVDF resin shall be Kynar using Kynar500/Hylar5000.
- Cleaned and pretreated with chromium phosphate
- Coat extrusions with approved primers to minimum dry film thickness of 0.20 mil (.0051 mm).
- Color coat shall be a minimum dry film thickness of 1.0 mil (.025 mm).
- Approved Coating Manufactures:
- PPG Industries
- Valspar Corporation
EXECUTION
- Do not begin installation until substrates have been properly prepared.
- If substrate preparation is the responsibility of another installer, notify Architect of unsatisfactory preparation before proceeding.
PREPARATION
- Clean surfaces thoroughly prior to installation.
- Prepare surfaces using the methods recommended by the manufacturer for achieving the best result for the substrate under the project conditions.
INSTALLATION
- Install in accordance with manufacturer's instructions.
FIELD QUALITY CONTROL
- Owner will engage an independent AAMA approved testing agency.
- Conduct test under the supervision of and in the presence of the Owner, Architect, and Construction Manager.
- Test wall in accordance with AAMA 501.2-94.
PROTECTION
- Protect installed products until completion of project.
- Touch-up, repair or replace damaged products before Substantial Completion.
Wind load design
Mullion deflection is limited per AAMA TIR-A11-04 deflection is limited to L/175 for spans up to 13'-6" and L/240 for spans beyond 13'-6"
allowable stress for 6063-T6 aluminum alloy = 15000 p.s.i. allowable stress for A-36 steel = 21600 p.s.i.
maximum deflection was based on the following equation:
Dead load design
maximum bending moment was based on the following equation:assumptions:
W = total uniform loadL = length of mullion between anchors E = 10 X 106 p.s.i.
I = moment of inertia of the mullion M = maximum bending moment
* mullions are assumed to have equal size glass lights each side check with local code requirements for acceptance of AAMA TIR-A11